Quality assurance in laser plastic welding I – where do errors occur?
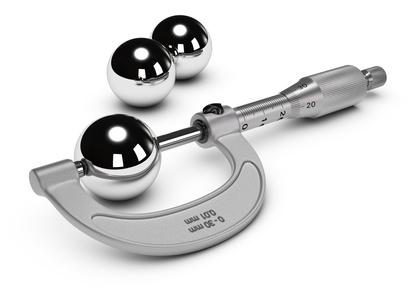
Laser welding of plastics is a very robust and reliable process. The causes of defective welds are mostly found in pre-processes along the value chain. Already in the first step, the compounding, the material components and thus the important optical properties are determined. Although the usual fluctuations in this step do not pose a problem, significant changes in material composition must be excluded. A change in color, fillers or reinforcing materials can have a significant impact on the quality of the weld. In practice, the injection molding process is much more relevant for the occurrence of defects. On the one hand, it has an enormous impact on the optical properties due to mold geometry and temperature control. Fiber and filler distributions in the component are defined and in the case of semi-crystalline plastics, the mold temperature determines the formation of crystalline structures. The transmission of the laser-transparent joining partner is thus directly influenced. On the other hand, injection molding determines the dimensional accuracy and surface quality, also important points for a successful welding process.