Quality assurance II – How to detect defects before welding?
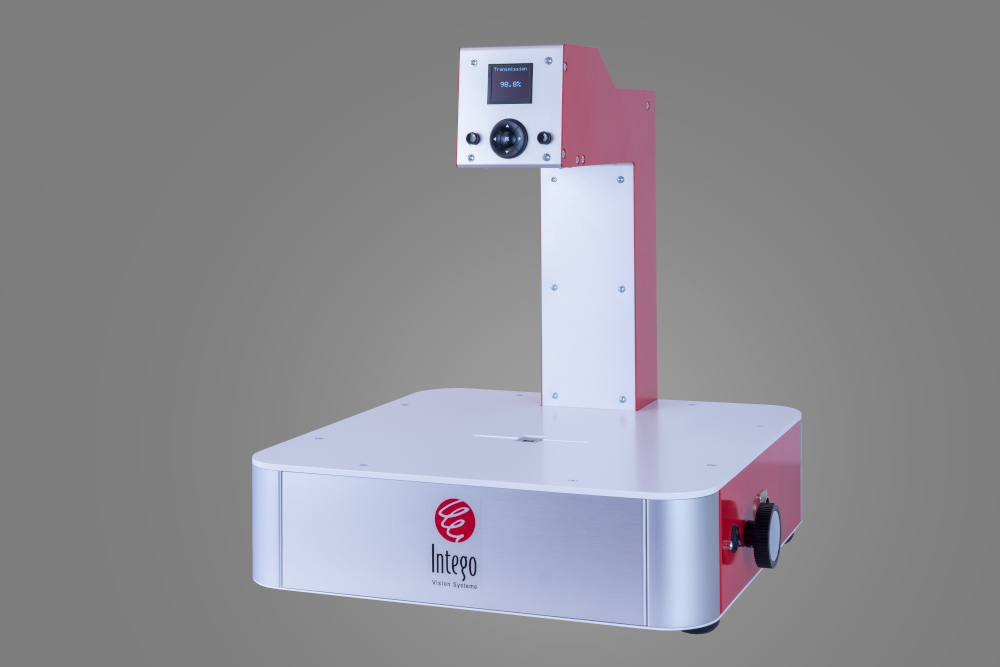
In order to keep defect costs in production low, it is useful to detect defects from pre-production before the welding process so that the corresponding components can be sorted out. In laser welding, by far the most frequent cause of defects is due to highly fluctuating transmission values of the laser-transparent joining partner.
For laser welding of plastics, mainly lasers with wavelengths in the near infrared are used, which are not visible to the human eye. As a result, visual inspection of components before welding is not possible. Special measuring devices, such as the TMS devices from Intego GmbH, offer the most reliable option here for detecting transmission variations. The basic principle is based on the fact that a laser beam shines through the component onto a detector and thus the transmission is determined. The devices are used either for manual random inspections or as a fully automatic 100% inspection. Components that are below a required transmission value can be safely sorted out.